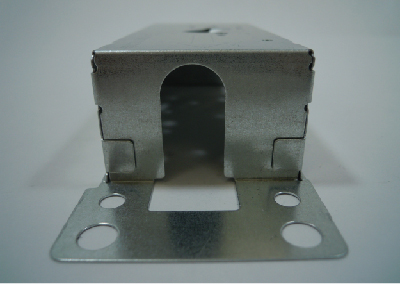
車載用電子機器ケースなどの箱型のプレス加工製品を成形する際、箱形状を保持するために四隅の締結が必要になります。プレス加工後に溶接工程に移動し、ロボット溶接機もしくはハンド溶接にて溶接します。また、四隅の溶接は歪みが発生しやすく、特にアルミ製品は溶接後に温度が下がる際に歪みが発生しやすいため、歪み取りの作業に時間がかかっていました。量産になればなるほど工数の増加がコスト上昇につながるため、加工工数削減によるコストダウンが必要でした。
四隅のカシメによる提携を可能とする金型を製作し、順送プレスにて成型することで、プレス工程内で製品形状の保持を行うことが可能になりました。四隅の溶接が不要になったことで、工程が短縮し製造リードタイムが短縮しました。工数が削減したことによりコストダウンも実現しました。また、四隅の溶接をなくしたことにより歪みの発生リスクを軽減し、歪み取り作業の発生による作業の長時間化を防ぎました。高橋金属は、金型設計・製造ノウハウを数多く持ち、自社で設計・製造した金型にてプレス加工を行っております。当事例のタッピング加工用金型についても、弊社にて設計・製造しました。
箱型形状の製品をプレス加工にて成型する場合、四隅の溶接作業をなくすために、順送プレス内にカシメによる締結を可能とする金型を搭載することにより工程を短縮できます。溶接作業が多くなると、歪みによる品質低下リスクが発生します。高橋金属では、工数削減と品質向上の観点から溶接作業を極力減らす工程を提案させて頂きます。プレス加工を持ちいた工数削減には、金型製作・設計技術やノウハウが必須です。これまで培ってきた技術とノウハウ、そして充実した設備を持って、ベストな生産方法をご提案させて頂きます。お気軽にお問合せください。
事例名称:段曲げ型製作により曲げ回数削減で製造リードタイム短縮
加工内容:板金加工
事例名称:位置決めエンボスやポンチ追加により溶接治具レスでコストダウン
加工内容:プレス加工
事例名称:プレス部品を鈑金形状に変更し金型製作・管理コストの削減
加工内容:プレス加工
事例名称:ファイバーレーザ溶接による溶融メッキ鋼板の重ね溶接で品質向上
加工内容:溶接加工
事例名称:ファイバーレーザ溶接による溶け落ちの無い突合せ溶接でコストダウン
加工内容:溶接加工
事例名称:ファイバーレーザ溶接による重ね溶接でむくれの削減、工程削減
加工内容:溶接加工
事例名称:プレス工程内のカシメ加工でコストダウン
加工内容:プレス加工 / 溶接加工
事例名称:プレス工程内のタッピング加工でコストダウン
加工内容:プレス加工
事例名称:自動車エンジン遮熱板プレス製品の同時取りでコストダウン
加工内容:プレス加工
事例名称:ZAM材を使用し、家庭用燃料電池スタックの製造コストダウン
加工内容:板金加工 / 溶接加工